Explosion-proof and anti-static design of valves are crucial factors in ensuring safe operations in certain specialized industrial environments. Below is a brief explanation of the principles behind explosion-proof and anti-static valve designs:
Explosion-proof Principle: Explosion-proof designs aim to prevent equipment from generating sparks, arcs, or high temperatures that could trigger explosions in environments with flammable gases, vapors, or dust.
Valve explosion-proof design might involve the following aspects:
- Isolation of Combustible Substances: Valves and their surroundings could utilize explosion-proof materials or enclosures to isolate flammable gases, liquids, or dust that could potentially cause explosions.
- Control of Electrostatic Discharges: Electrostatic discharges on valve surfaces could ignite explosions. Therefore, valves might incorporate conductive materials, grounding devices, etc., to control electrostatic discharge.
- Explosion-proof Sealing Design: The sealing design of valves should ensure that combustible substances are not leaked during operation, avoiding potential sparks or gas leaks.
- Explosion-proof Enclosures: In some cases, valves might be installed within explosion-proof enclosures to prevent the impact of shockwaves generated by explosions from affecting the surrounding environment.
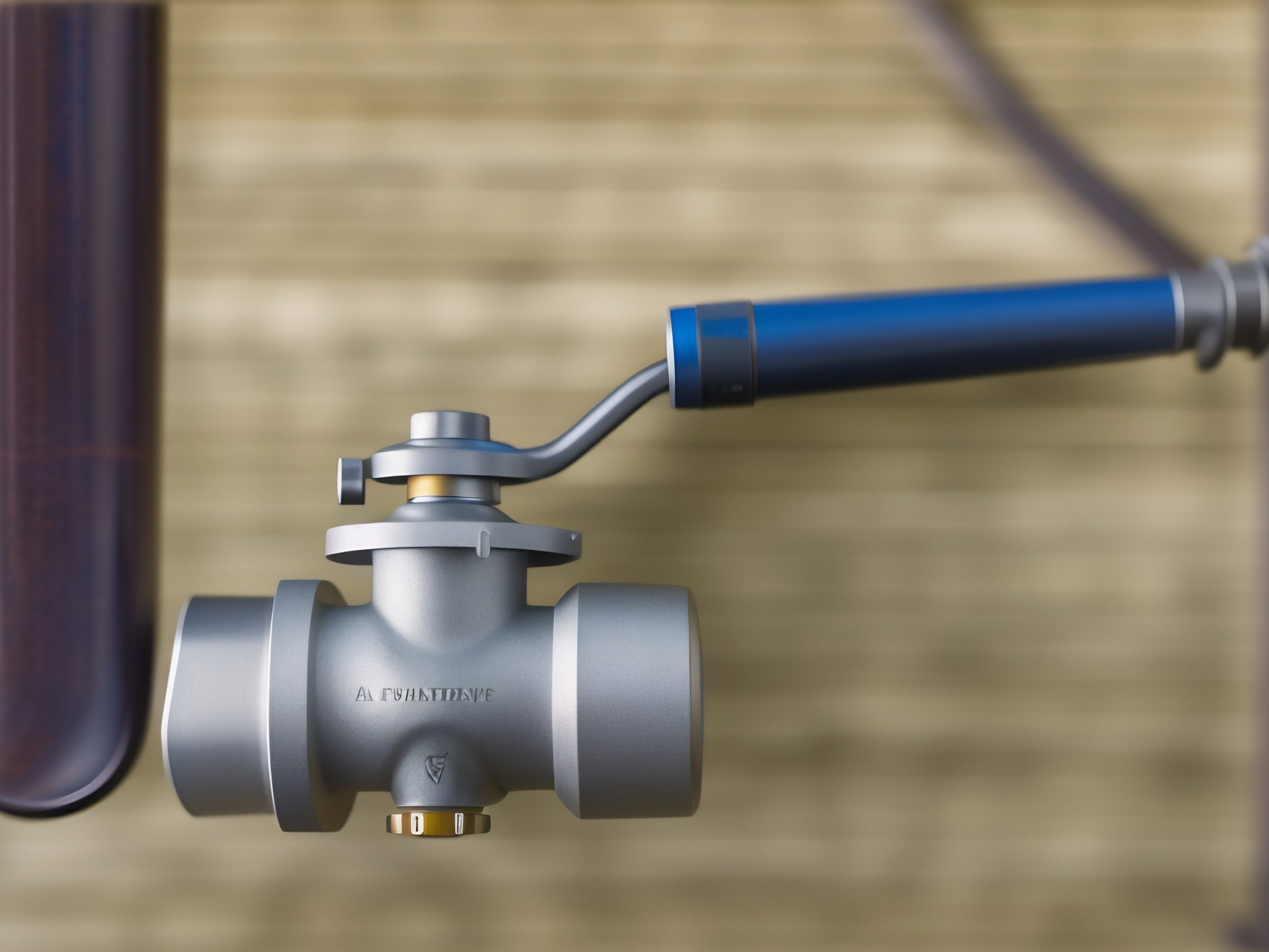
Anti-static Principle: Anti-static designs aim to control or eliminate sparks caused by accumulated static electricity, thereby reducing the risk of explosions.
Here are key aspects of anti-static design:
- Conductive Materials: Valve construction materials might include those with good conductivity to safely channel static charges to the ground, preventing static buildup.
- Grounding Systems: Valves might be connected to the grounding system of equipment or systems to safely discharge static charges to the ground.
- Anti-static Dischargers: Anti-static dischargers might be installed on valves. These devices can eliminate accumulated static charges by releasing gas or applying an electric field.
- Insulation Measures: Valves might use insulation materials or coatings to reduce the accumulation of static charges.
It’s important to note that explosion-proof and anti-static valve designs need to be customized based on specific industrial environments and application requirements. These principles find particularly crucial applications in high-risk industrial sectors such as petrochemical, oil and gas, where the presence of combustible gases, steam, dust, etc., demands enhanced safety measures.
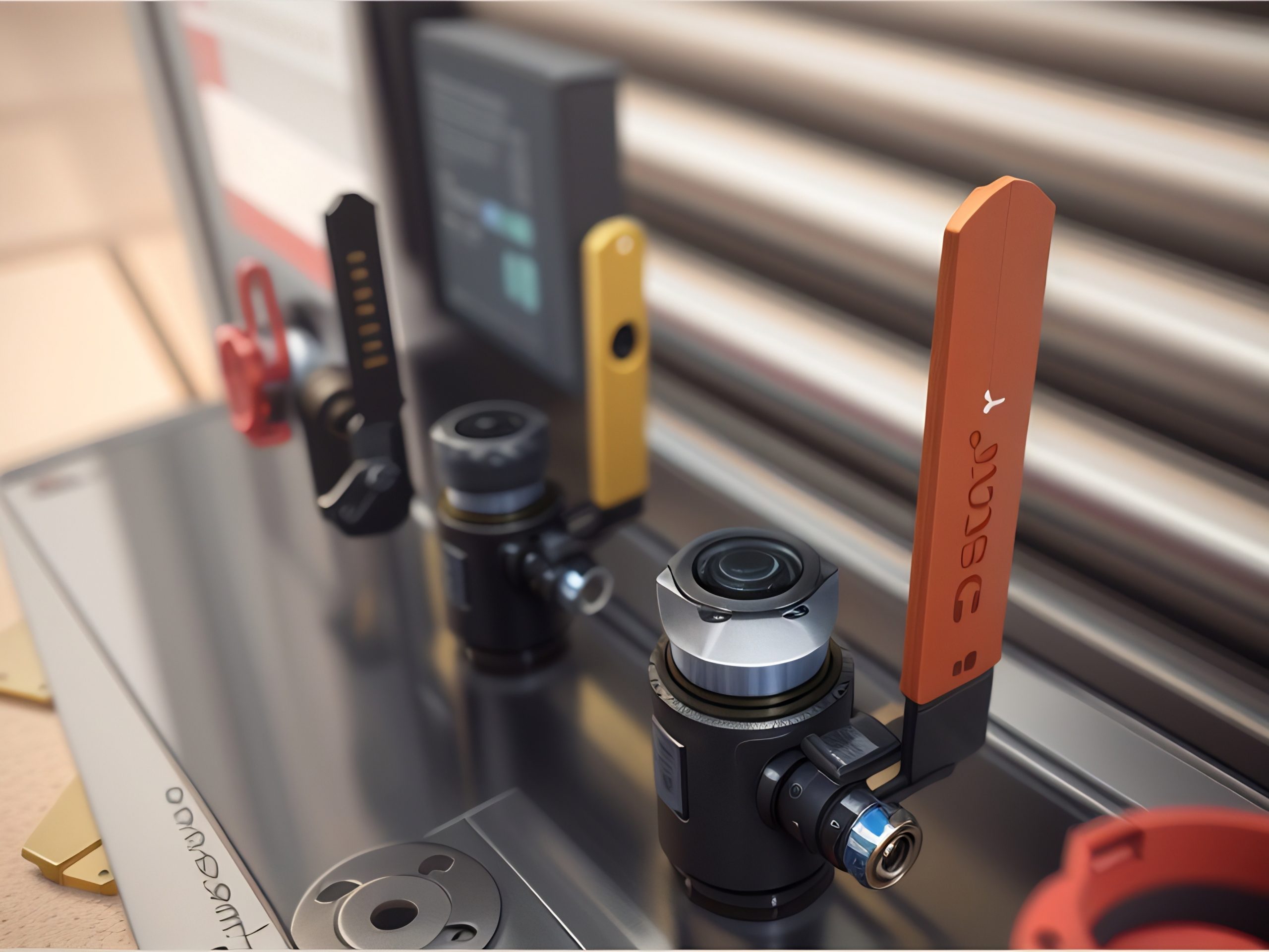
Valve explosion-proof and anti-static designs are primarily applied in industrial environments with combustible gases, vapors, dust, and similar hazardous substances.
Here are some specific fields and applications where explosion-proof and anti-static valves are essential:
- Oil and Gas Industry: In processes involving petroleum and natural gas extraction, storage, transportation, and processing, explosion-proof and anti-static valves are vital for controlling fluid flow within pipelines, tanks, and gas stations.
- Chemical Industry: Chemical plants handle various flammable and explosive chemicals, making explosion-proof and anti-static valves critical for controlling fluid and gas flow to prevent sparks that could lead to explosions.
- Dusty Environments: Some industries, like flour processing and coal handling, generate significant amounts of dust, which could ignite under certain conditions. Explosion-proof and anti-static valves control the transfer and handling of dust in such environments.
- Mining: Mines might contain combustible gases and dust, such as coal mines and metal mines. Explosion-proof and anti-static valves ensure safe operations during mining and processing.
- Pharmaceutical Industry: Flammable solvents and chemicals might be involved in pharmaceutical processes, and explosion-proof and anti-static valves help ensure the safety of production processes.
- Paint and Coating Production: Manufacturing paint and coatings involves volatile solvents that could trigger explosions. Explosion-proof and anti-static valves control solvent flow and storage.
- Aerospace Industry: Aerospace manufacturing involves special materials and processes that can generate static electricity. Anti-static valves control material flow and prevent sparks from causing explosions.
- Liquefied Natural Gas (LNG) Industry: In the LNG industry, which deals with the storage and transportation of liquefied gases, explosion-proof and anti-static valves play a critical role in ensuring safe operation of LNG facilities.
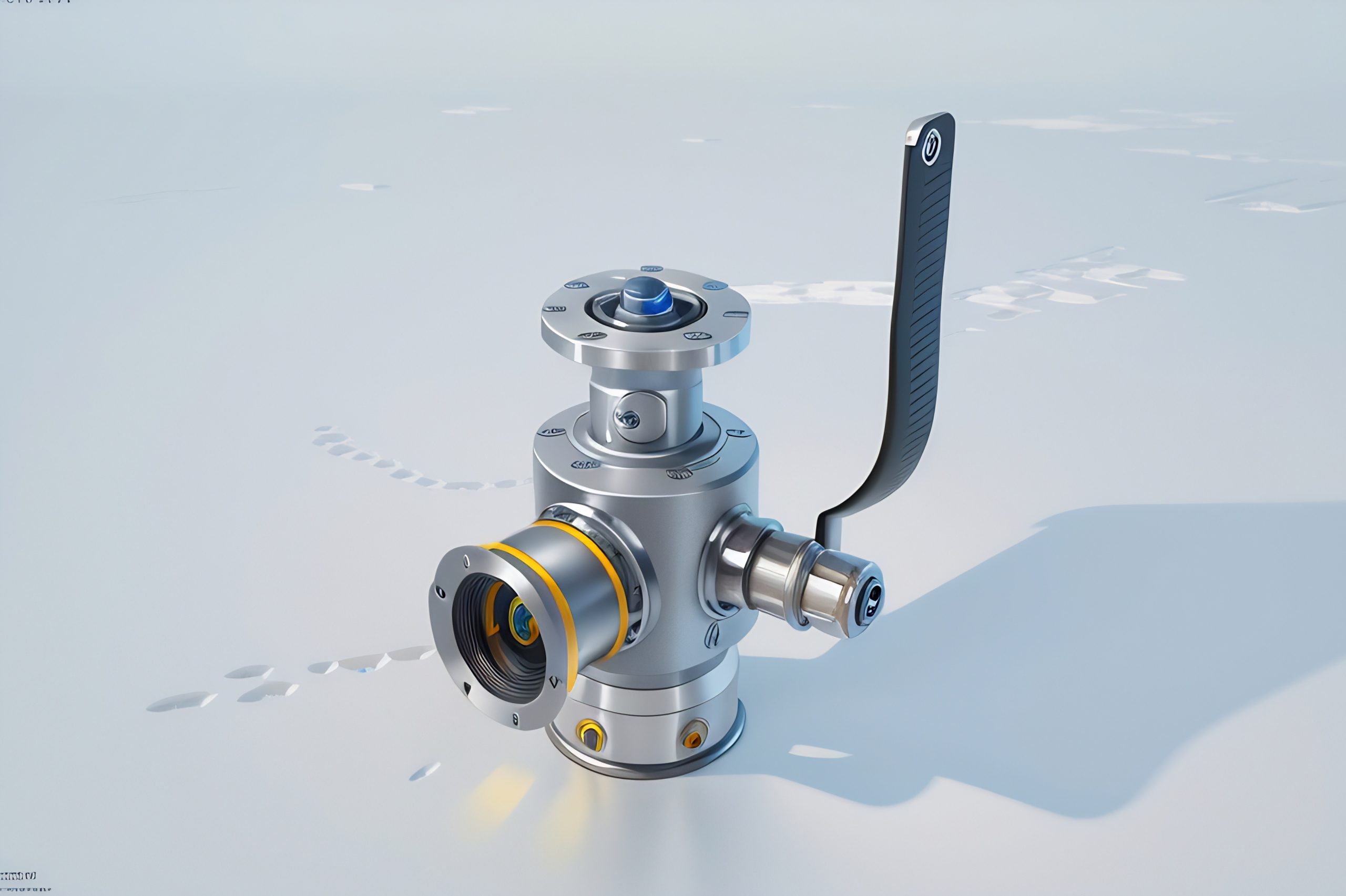
These are just a few examples; in reality, explosion-proof and anti-static valves can find applications in many industries that require the control of fluids and gases. In these fields, explosion-proof and anti-static designs help minimize the risk of fires and explosions, ensuring the safety of personnel and equipment.