The structural characteristics of a floating ball valve are as follows:
The floating ball valve achieves its on-off action by using two seat sealing rings at the inlet and outlet to clamp the central ball core. By rotating the valve stem, the ball core is turned 90° to facilitate the opening and closing of the ball valve. When the ball core is in the closed position, the semi-circular shape at the top of the valve stem aligns with the semi-circular groove of the ball core. Under the influence of medium pressure, the ball core moves toward the outlet, hence earning the designation “floating ball valve.”
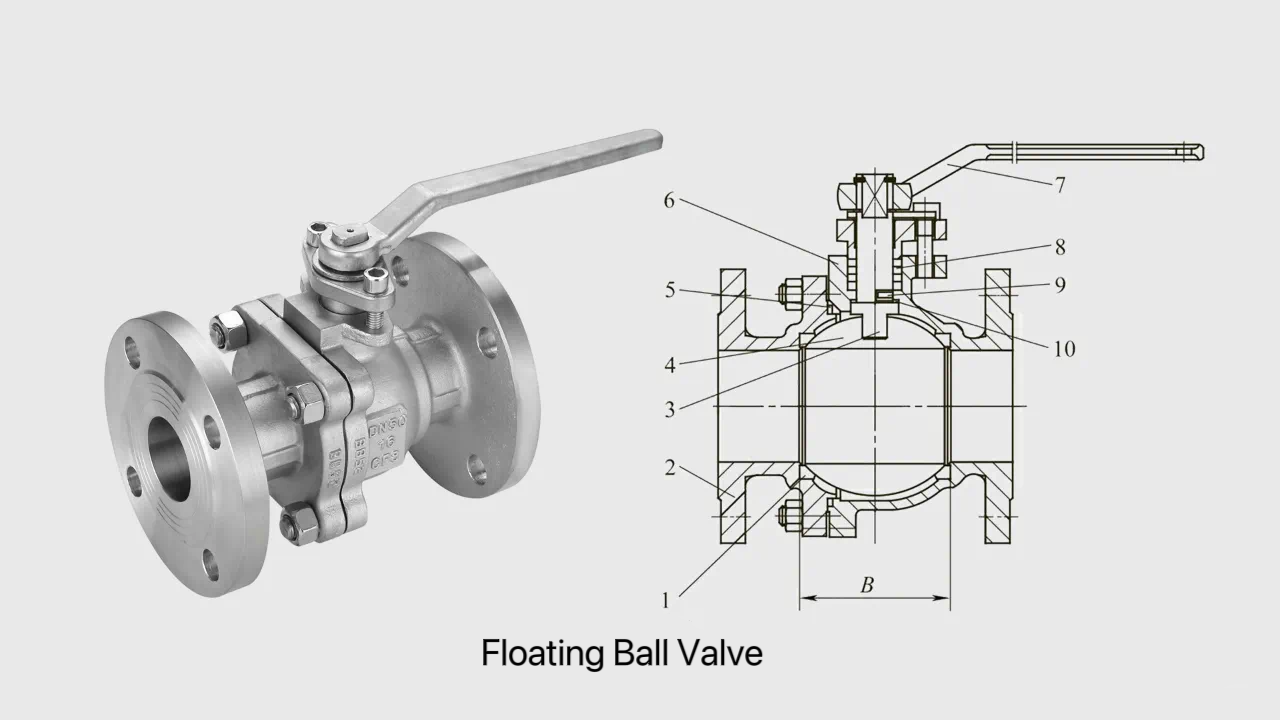
The inlet and outlet valve seats have a certain pre-tightening force to envelop the ball core. When the valve is closed, the medium pressure propels the ball core, causing it to tightly press against the sealing ring of the outlet valve seat. This enhances the sealing of the outlet valve seat, ensuring the overall sealing performance of the ball valve.
In addition to the load generated by the pre-tightening pressure on the seat of the floating ball valve, consideration must be given to the load from the self-weight of the ball core and the pressure of the medium pushing the ball core, which applies pressure to the outlet valve seat. This is particularly crucial in high-pressure and large-diameter ball valves. It is essential to avoid exceeding the allowable stress of the seat material, preventing damage caused by the pressure of the ball core and avoiding occurrences of internal leakage.
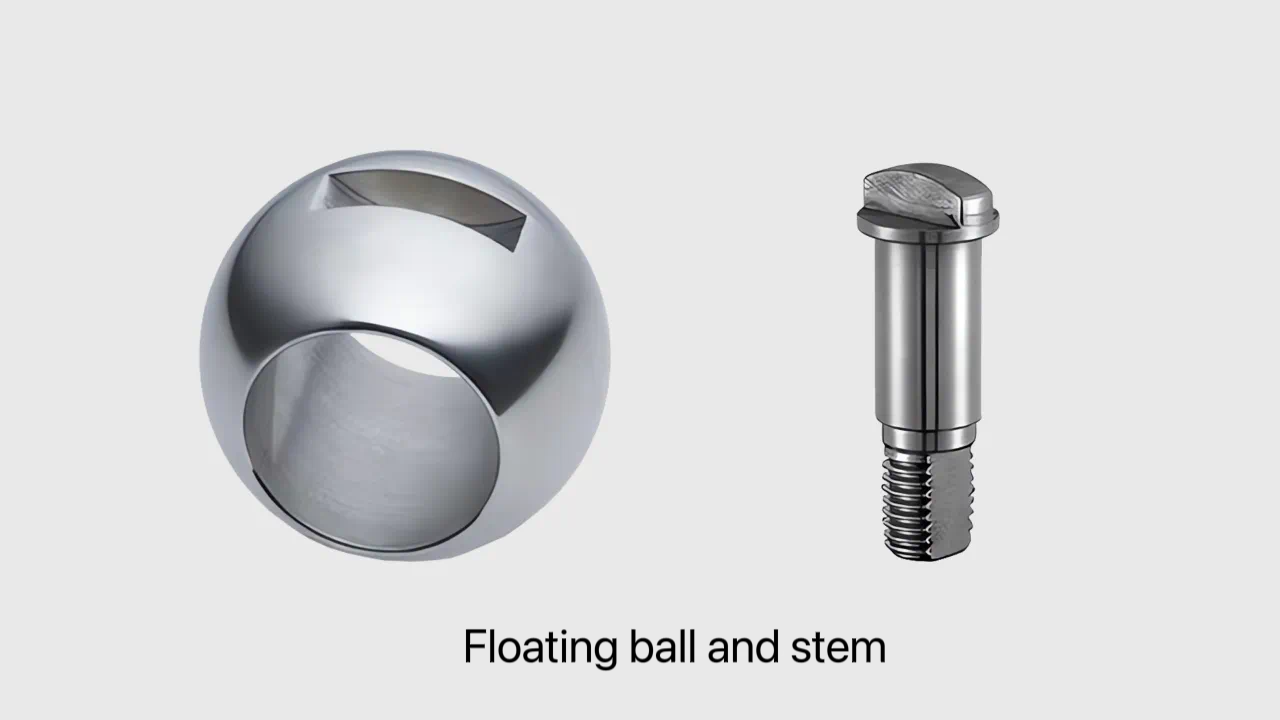
Common materials for valve seats include PTFE (polytetrafluoroethylene), PPL (polyphenylene), nylon, PEEK (polyetheretherketone), and metal hard sealing, among others.
The structural features of a fixed ball valve are as follows:
The fixed ball valve also features two seat sealing rings at the inlet and outlet. The central ball core is fixed to the valve body through the upper and lower valve stems. The opening and closing action of the ball core can only be achieved through the rotation of the valve stem. Unlike the floating ball valve, the fixed ball valve cannot move towards the outlet, as the movement of the ball core is restricted by the upper and lower valve stems. Hence, it is referred to as a fixed ball valve.
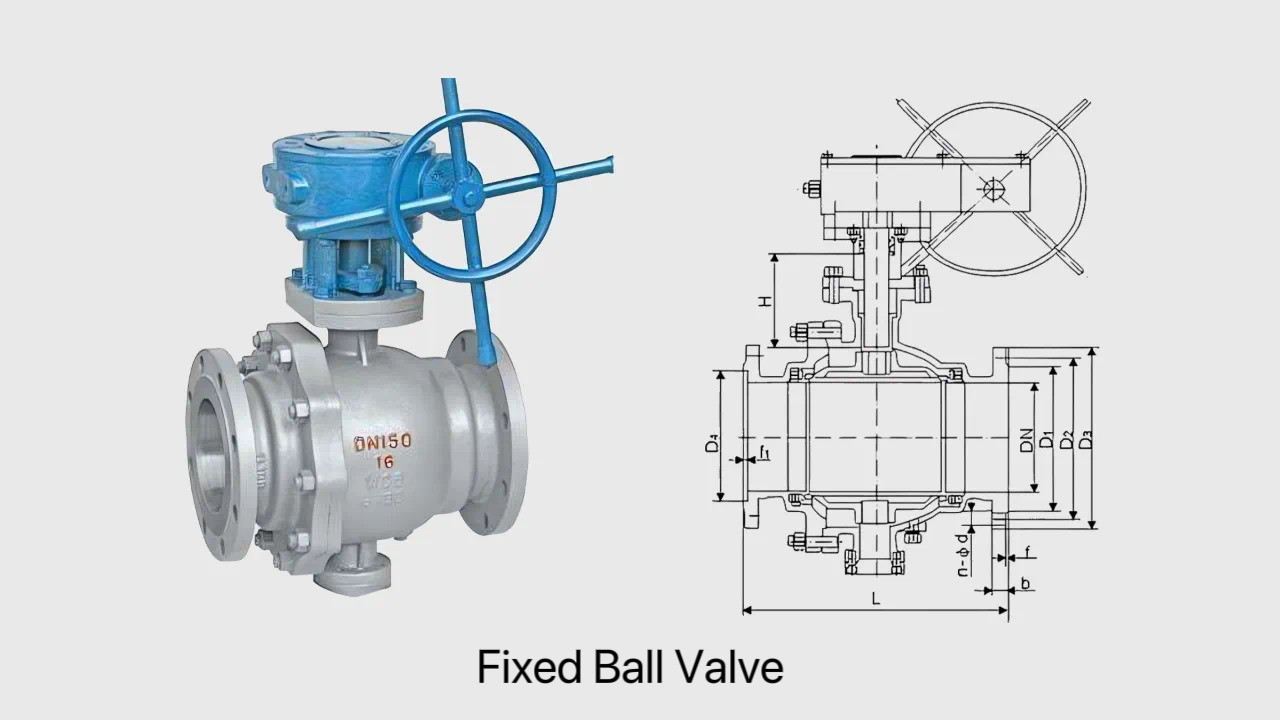
The inlet and outlet valve seats are initially sealed with a pre-tightening force provided by a spring, creating an initial sealing pressure between the ball core and the valve seat. The pressure of the medium propels the sealing ring of the valve seat to press against the ball core, enhancing the sealing performance of the valve seat. In cases where the valve seat experiences wear, the spring automatically compensates for the worn parts, ensuring continued effective sealing under the influence of the spring.
Due to the circular cross-section of the valve seat, the area subjected to medium pressure is smaller than the cross-sectional area of the ball core. As a result, the pressure on the valve seat is less than that in a floating ball valve. This reduction in pressure contributes to a decrease in the torque required for the valve stem. Therefore, in high-pressure and large-diameter ball valves, fixed ball valves are commonly employed.
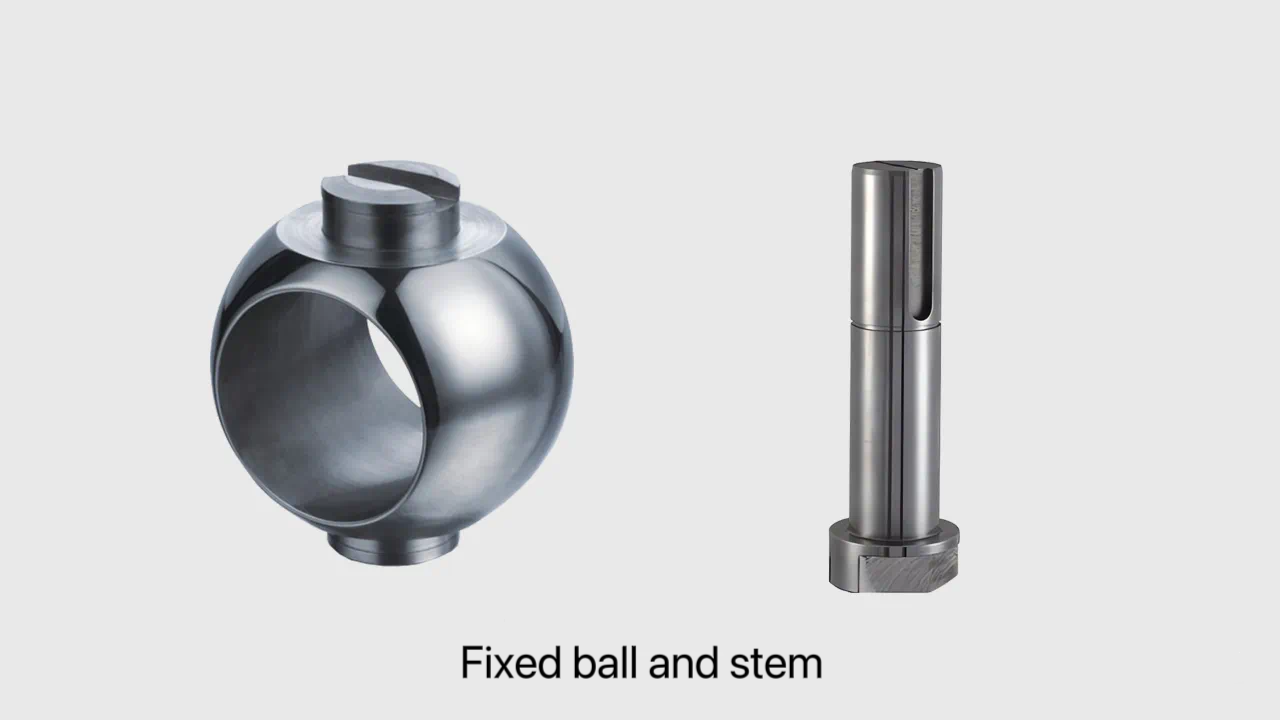
DBB, which stands for Double Block and Bleed, features a single-piston effect valve seat structure. When there is pressure at both the inlet and outlet simultaneously, it can achieve the dual-shutoff function. Additionally, it has a middle cavity pressure relief function. In the event of an abnormal increase in pressure in the middle cavity, the medium pressure can push the valve seat away from the ball core, releasing the pressure in the middle cavity into the pipeline, ensuring the safety of the ball valve.
DIB-I, which stands for Double Isolation and Bleed with a dual-piston effect valve seat structure, maintains sealing for both inlet pressure, outlet pressure, or middle cavity pressure, achieving dual isolation functionality. The valve body’s middle cavity is equipped with a pressure relief valve that automatically releases pressure when the middle cavity pressure exceeds 1.33 times the design pressure.
DIB-II features a combination of a single-piston effect valve seat and a dual-piston effect valve seat. The fixed ball valve has a sealed grease injection port at the valve seat and stem positions. This helps enhance sealing, reduce seal surface wear, extend the lifespan, and provide more time for maintenance in the event of leakage at the ball valve outlet.
The differences between a floating ball valve and a fixed ball valve as follow:
Different Sealing Structures:
Floating Ball Valve: The ball core can move along the flow channel, while the valve seat remains stationary. It has only an upper valve stem, allowing the ball core to move along the flow channel direction. The medium pressure drives the ball core to press against the outlet valve seat, achieving unilateral forced sealing.
Fixed Ball Valve: The ball core has both upper and lower valve stems, fixing it to the valve body. The ball core cannot move along the flow channel direction. Sealing is achieved by moving the valve seat to grip the ball core.
Different Application Conditions:
Floating Ball Valve: Primarily used for low pressure and small diameters. At high pressures, the medium pushing the ball core can damage the outlet valve seat and increase the torque of the ball valve.
Fixed Ball Valve: Mainly used for high pressure and large diameters. For example, in the West-East Gas Pipeline, where pressures can reach 1500LB and diameters can be up to DN1500mm. The structure of the valve seat pressing against the ball core helps reduce seat sealing pressure and decrease the torque of the ball valve.
Different Seat Sealing:
Fixed Ball Valve: Can achieve various seat sealing functions, including front unidirectional sealing, rear unidirectional sealing, front bidirectional sealing, rear bidirectional sealing, and middle cavity pressure relief.
Floating Ball Valve: Relies on the outlet valve seat to achieve forced sealing.