What exactly are ‘steel’ and ‘iron,’ what are their characteristics, and what is their relationship? Additionally, how are terms like 304, 304L, 316, and 316L derived, and what are the differences between them?
Steel: a material primarily composed of iron, with a carbon content generally below 2%, and containing other elements. Iron: a metallic element with the atomic number 26. Iron materials exhibit strong ferromagnetism, along with good malleability and conductivity. Stainless Steel: a type of steel that resists corrosion in weak corrosive media such as air, steam, and water. Commonly used grades include 304, 304L, 316, and 316L, which belong to the austenitic stainless steel 300 series.
304 Stainless Steel:
Performance Overview
304 stainless steel is the most common type, widely known for its good corrosion resistance, heat resistance, low-temperature strength, and mechanical properties. It exhibits excellent hot working properties like stamping and bending, without experiencing hardening due to heat treatment (non-magnetic, usable in temperatures ranging from -196°C to 800°C).
Applications
- Household items (Class 1 and 2 tableware, cabinets, indoor pipelines, water heaters, boilers, bathtubs).
- Automotive parts (windshield wipers, mufflers, molded products).
- Medical equipment, construction materials, chemical, food industry, agriculture, and ship components.
304L Stainless Steel:
(L denotes low carbon)
Performance Overview
As a low-carbon variant of 304 steel, its corrosion resistance is similar to 304 in general conditions. However, after welding or stress relief, it exhibits excellent resistance to intergranular corrosion. It maintains good corrosion resistance without heat treatment, usable in temperatures ranging from -196°C to 800°C.
Applications
Used in industries like chemical, coal, and petroleum that demand high resistance to intergranular corrosion, outdoor machinery, heat-resistant parts in construction materials, and parts with challenging heat treatment.
316 Stainless Steel:
Performance Overview
316 stainless steel, with the addition of molybdenum, excels in corrosion resistance, resistance to atmospheric corrosion, and high-temperature strength. It can be used in harsh conditions and has superior work hardening properties (non-magnetic).
Applications
Equipment for use in seawater, production equipment for chemicals, dyes, papermaking, oxalic acid, fertilizers, photography, food industry, coastal facilities, ropes, CD rods, bolts, and nuts.
316L Stainless Steel:
(L denotes low carbon)
Performance Overview
As a low-carbon series of the 316 steel, it shares the same characteristics but has superior resistance to intergranular corrosion.
Applications
Products with specific requirements for resistance to intergranular corrosion.
Performance Comparison
Chemical Composition
316 and 316L stainless steels are molybdenum-containing stainless steel types. The molybdenum content in 316L stainless steel is slightly higher than in 316 stainless steel. Due to the addition of molybdenum, these steels outperform 310 and 304 stainless steels in overall performance. In high-temperature conditions, 316 stainless steel finds extensive applications when the concentration of sulfuric acid is below 15% or above 85%. 316 stainless steel also exhibits good resistance to chloride corrosion, making it suitable for marine environments. The maximum carbon content in 316L stainless steel is 0.03, making it suitable for applications requiring maximum corrosion resistance after welding and cannot undergo annealing.
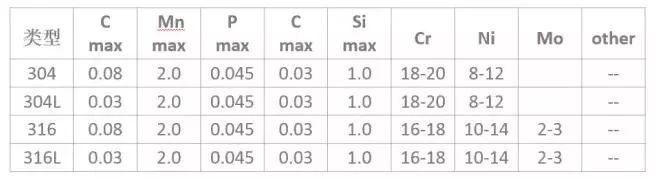
Corrosion Resistance
316 stainless steel has better corrosion resistance than 304 stainless steel, especially in the production processes of pulp and paper. Additionally, 316 stainless steel resists corrosion in marine environments and corrosive industrial atmospheres.
In general, there is not much difference in the chemical corrosion resistance between 304 and 316 stainless steel. However, there are specific differences in certain media.
The initial development of stainless steel was 304, which, in specific conditions, is sensitive to pitting corrosion. The addition of 2-3% molybdenum reduces this sensitivity, giving rise to 316. Moreover, this additional molybdenum also reduces the corrosion of certain hot organic acids.
316 stainless steel has almost become the standard material in the food and beverage industry. Due to the global shortage of molybdenum and higher nickel content in 316 stainless steel, it is more expensive than 304 stainless steel.
Pitting corrosion is mainly caused by surface-deposited corrosion on stainless steel due to lack of oxygen, preventing the formation of a chromium oxide protective layer.
Especially in small valves, the likelihood of deposits on the valve plate is low, so pitting corrosion is rare.
In various types of water media (distilled water, drinking water, river water, boiler water, seawater, etc.), the corrosion resistance of 304 stainless steel and 316 stainless steel is almost the same, unless the chloride ion content in the medium is very high, in which case 316 stainless steel is more suitable.
In most cases, there is not much difference in corrosion resistance between 304 stainless steel and 316 stainless steel. However, in some situations, the difference may be significant and requires a specific analysis of the circumstances. Generally, valve users should be aware, as they will choose materials for containers and pipes based on the medium’s conditions, and it is not advisable to recommend materials to users.
Heat Resistance
316 stainless steel has good oxidation resistance in intermittent use below 1600 degrees and continuous use below 1700 degrees. It is advisable not to continuously use 316 stainless steel in the range of 800-1575 degrees, but when used continuously outside this temperature range, the stainless steel has good heat resistance. The performance of 316L stainless steel in resisting carbide precipitation is better than that of 316 stainless steel and can be used in the mentioned temperature range.
Heat Treatment
Annealing is performed in the temperature range of 1850-2050 degrees, followed by rapid annealing and then rapid cooling. 316 stainless steel cannot undergo over-heat treatment for hardening.
Welding
316 stainless steel has good welding performance and can be welded using all standard welding methods. Depending on the application, 316Cb, 316L, or 309Cb stainless steel filler rods or electrodes can be used for welding. For the best corrosion resistance, the welded section of 316 stainless steel requires post-weld annealing treatment. If using 316L stainless steel, post-weld annealing treatment is not necessary.
Mechanical Properties
Among all steels, austenitic stainless steel has the lowest yield point. Therefore, considering mechanical properties, austenitic stainless steel is not the optimal material for valve stems because, to ensure a certain strength, the diameter of the valve stem would need to increase. The yield point cannot be increased through heat treatment but can be improved through cold forming.
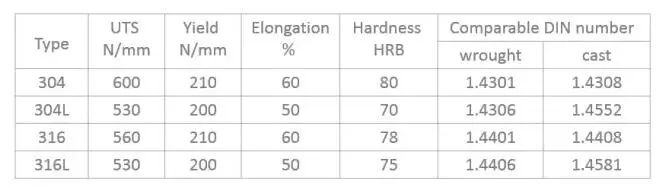
Magnetism
Due to the widespread use of austenitic stainless steel, there is a misconception that all stainless steels are non-magnetic. For austenitic stainless steel, it can generally be understood as non-magnetic, especially in the case of annealed forged steel. However, 304 subjected to cold forming may exhibit some magnetism. For cast steel, if it is 100% austenitic stainless steel, it is non-magnetic.
Low Carbon Types of Stainless Steel
The corrosion resistance of austenitic stainless steel comes from the chromium oxide protective layer formed on the metal surface. If the material is heated to high temperatures between 450°C and 900°C, a structural change occurs, and chromium carbide forms along the grain boundaries. This prevents the formation of the chromium oxide protective layer along the crystal edges, resulting in a decrease in corrosion resistance. This type of corrosion is known as “intergranular corrosion.”
To combat this corrosion, 304L stainless steel and 316L stainless steel were developed. Both 304L and 316L stainless steels have lower carbon content, which prevents the formation of chromium carbide and, consequently, avoids intergranular corrosion.
It’s important to note that higher sensitivity to intergranular corrosion does not necessarily mean that non-low carbon materials are more prone to corrosion. This sensitivity is particularly heightened in high-chloride environments.
It’s worth mentioning that this phenomenon occurs at elevated temperatures (450°C-900°C), often associated with welding. For typical soft-seated conventional butterfly valves, where welding operations are not performed on the valve plate, using low carbon stainless steel may not have significant implications. However, many specifications may still recommend 304L or 316L stainless steel.