V-type ball valves have a V-shaped opening on one side of the hemisphere valve core. By adjusting the opening of the valve core, the cross-sectional area of the medium flow can be changed. These valves are used for regulating flow and can also be employed for on-off control to open or close pipelines. They have a self-cleaning function and can achieve precise flow control within a small opening range. With a high turndown ratio, they are suitable for media containing fibers, fine particles, and slurry. The V-type ball valve is designated by the code VQ, and it follows the design standard JB/T 13517.
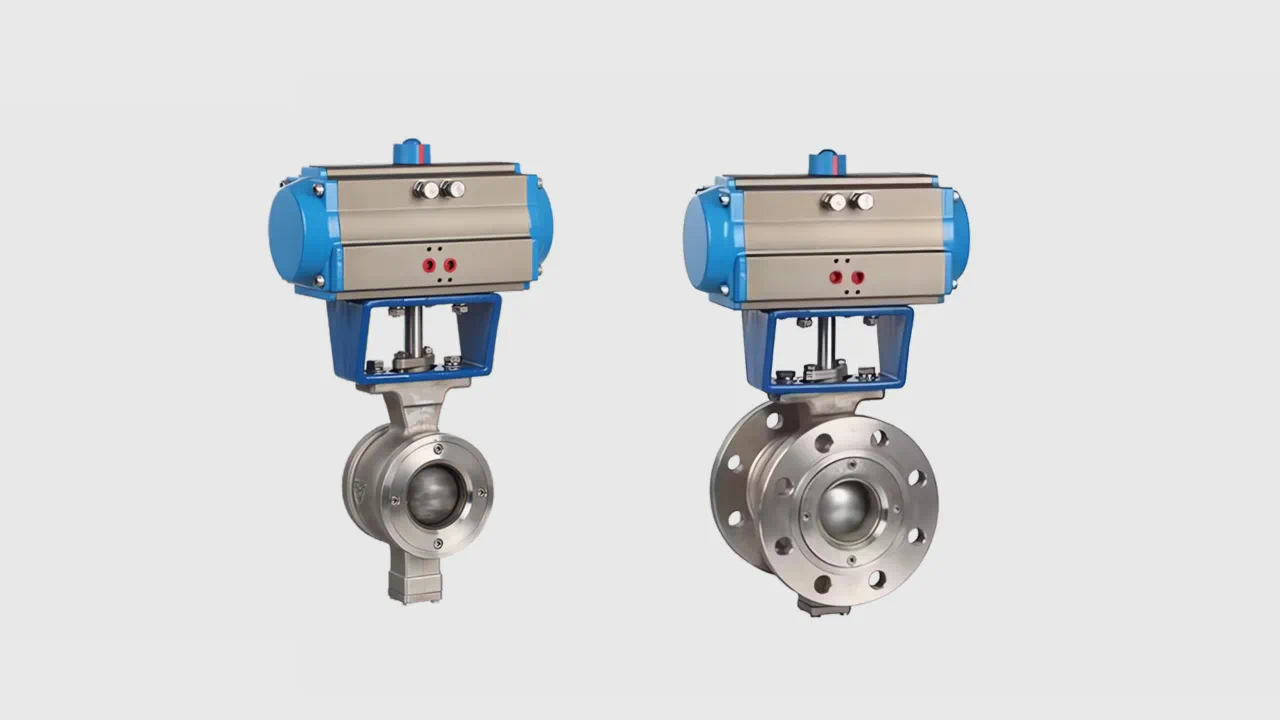
The structural characteristics can be summarized as follows:
1.Low fluid resistance, high flow coefficient, and a high turndown ratio of up to 100:1, which is significantly greater than the typical 30:1 turndown ratio of straight-through single-seated control valves, double-seated control valves, and sleeve control valves. The flow characteristic is approximately equal percentage.
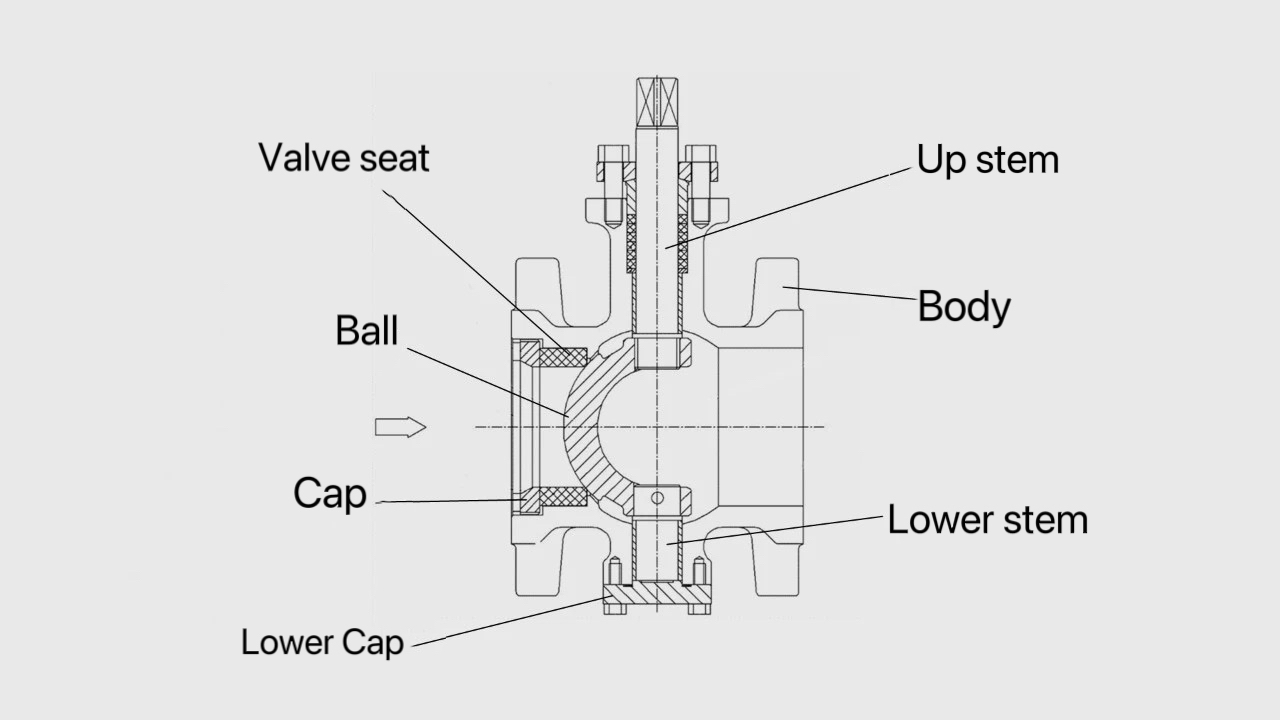
2.Reliable sealing: The leakage level of the metal hard-seal structure is rated as Class IV according to GB/T4213 “Pneumatic Control Valve.” For the soft-seal structure, the leakage level is rated as Class V or VI according to GB/T4213. In the case of a hard-seal structure, various processes such as hard chrome plating, cobalt-based hard alloy welding, and spraying tungsten carbide wear-resistant coating can be applied to the ball core sealing surface to enhance the service life of the valve core seal.
3.Quick opening and closing: V-type ball valves are classified as rotary valves with a 90° rotation angle from fully open to fully closed. When equipped with an AT piston-type pneumatic actuator, they can be used for rapidly shutting off flow conditions. Adding an electric valve positioner allows for proportional adjustment based on analog signals in the range of 4-20mA.
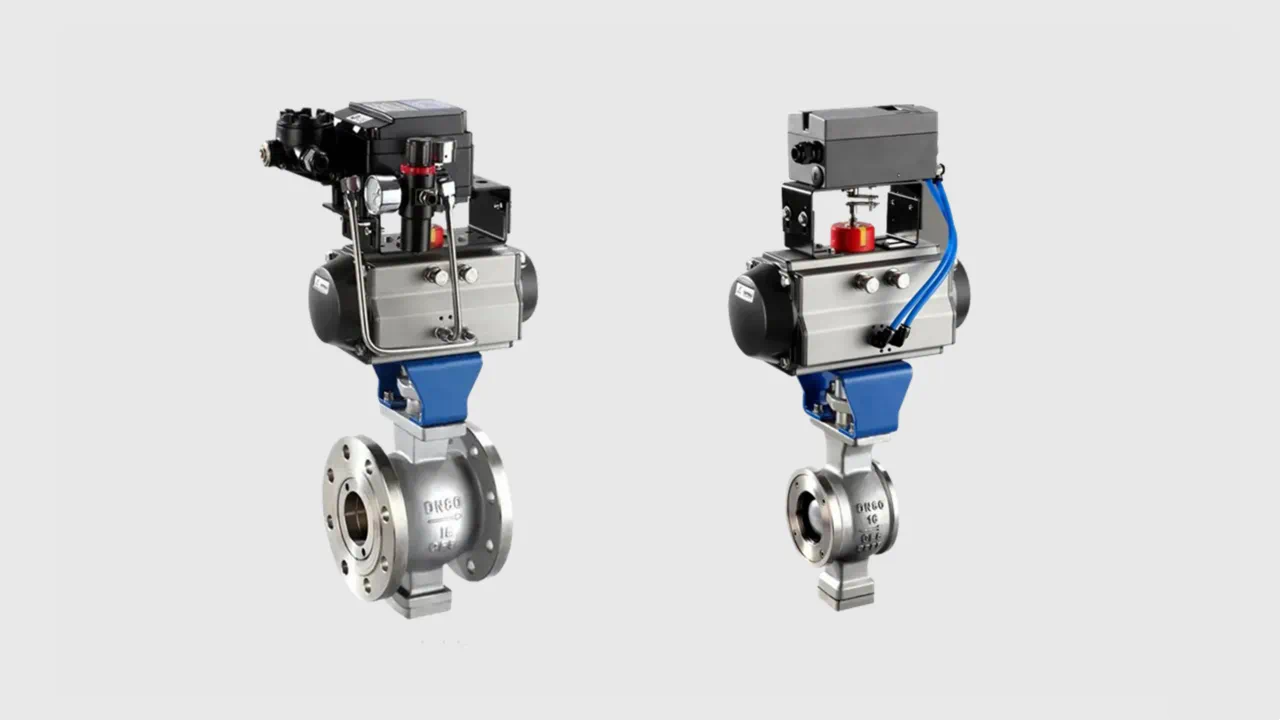
4.Excellent anti-blocking performance: The valve core adopts a 1/4 spherical shape, combined with a single-sided valve seat structure. In the presence of solid particles in the medium, it won’t experience the central cavity blockage issue that is common in ordinary O-type ball valves. The V-shaped ball and valve seat rotate without any gap, generating significant shear force, making it particularly suitable for controlling suspensions with fibrous or tiny solid particles, as well as solid particulate matter. Additionally, there are V-type ball valves with a full spherical valve core, which are more suitable for high-pressure conditions and can effectively reduce deformation of the ball core under high-pressure differentials. They use a single-seat or double-seat sealing structure. Double-seat sealed V-type ball valves are often used for clean medium flow control, as particles in the medium can pose a risk of central cavity blockage.

5.V-type ball valves feature a fixed ball structure with a spring-loaded valve seat that can move along the flow direction. This design allows for automatic compensation of ball core wear, extending the valve’s lifespan. Various types of springs, such as hexagonal springs, wave springs, disc springs, and cylindrical compression springs, can be used. When the medium contains fine impurities, it’s essential to add sealing rings to protect the springs and prevent their failure due to impurities. For V-type ball valves with a double-seat sealed full-spherical valve core, a floating ball structure is employed.
6.In applications where fire resistance and anti-static properties are required, the valve core adopts a metal hard-seal structure, and the packing uses high-temperature-resistant materials like flexible graphite. The valve stem is equipped with a sealing shoulder. Measures are taken to discharge static electricity between the valve body, valve stem, and ball. This design complies with GB/T26479 for fire-resistant structures and GB/T12237 for anti-static requirements.
7.V-type ball valves come in different structures based on the sealing of the ball core, including zero eccentricity, single eccentricity, double eccentricity, and triple eccentricity structures. The commonly used structure is the zero eccentric type. The use of eccentric structures allows the valve core to quickly detach from the valve seat during opening, reducing wear on the sealing ring and extending the lifespan. During closure, an eccentric force is generated to enhance the sealing effect.
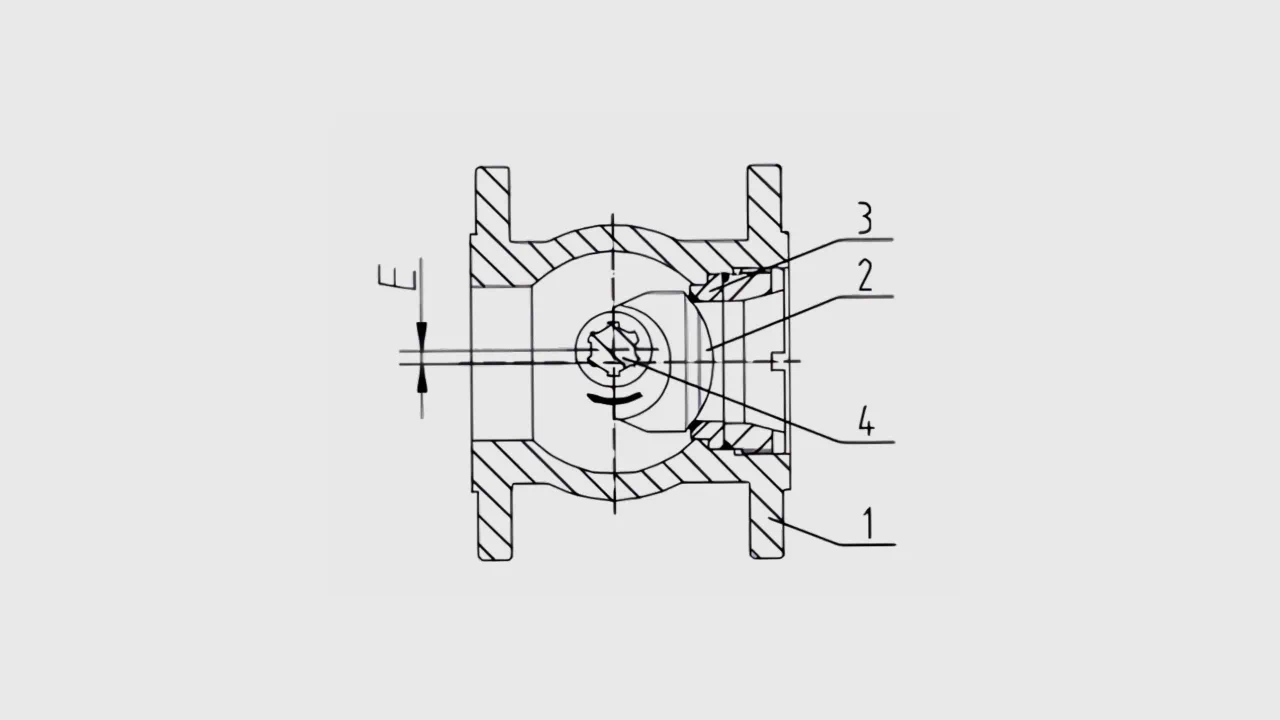
8.V-type ball valves can be operated through various driving methods, including manual (handled), worm gear, pneumatic, electric, hydraulic, and electro-hydraulic linkage systems.
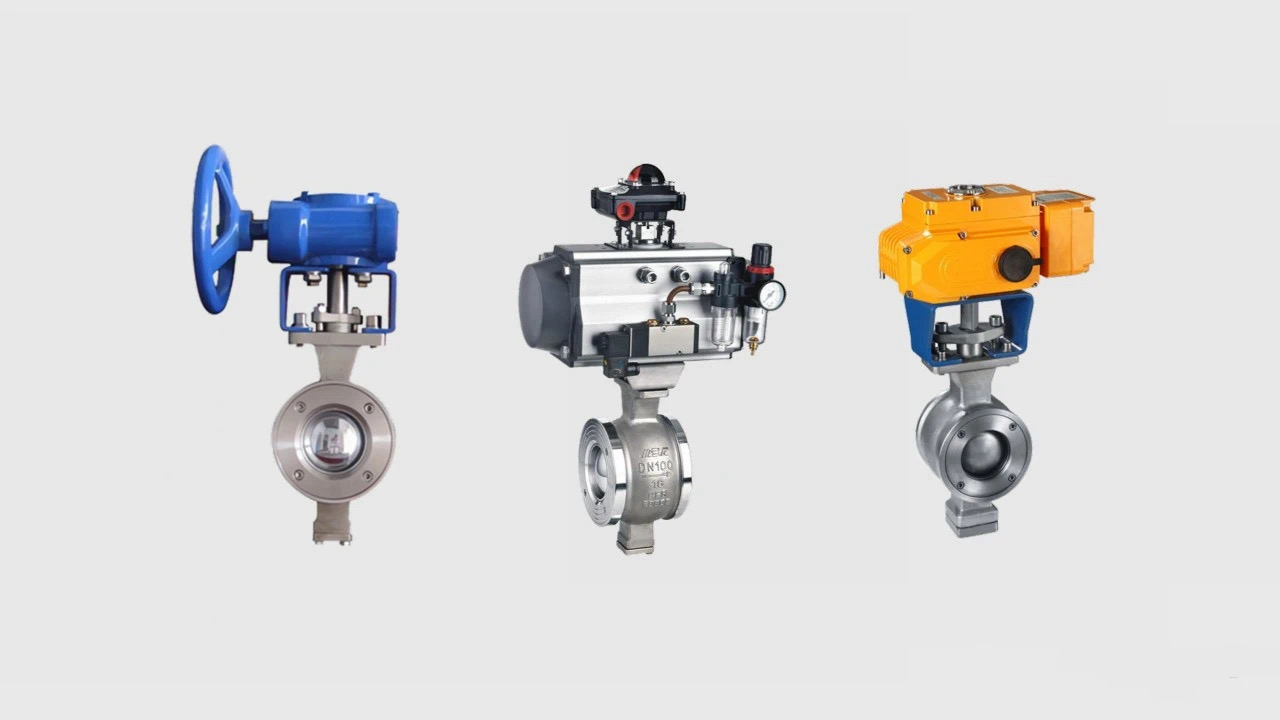
9.V-type ball valves can be connected through flange connection and clamp connection. For full-spherical valve cores with double-seat sealed structures, threaded connection, socket welding, and butt welding are additional connection options.
10.Ceramic ball valves also feature a V-type ball core structure. They exhibit excellent wear resistance and are resistant to acid and alkali corrosion, making them particularly suitable for regulating control with particle-containing media. Fluorine-lined ball valves also have a V-type ball core structure, used for regulating control in corrosive acid and alkali environments. The application scope of V-type ball valves is becoming increasingly diverse.